Choosing the Best Defoamers for Your Manufacturing Line
Choosing the Best Defoamers for Your Manufacturing Line
Blog Article
Discover the Leading Advantages of Using Defoamers in Industrial Processes
The utilization of defoamers in industrial processes offers an array of compelling benefits that can enhance operational performance and item top quality. By efficiently regulating foam manufacturing, these agents not just maximize material flow yet likewise contribute to substantial expense decreases and boosted sustainability. The implications of adopting defoamers might be extra profound than at first perceived.
Improved Process Performance
Optimizing industrial procedures commonly entails resolving lathering issues, which can impede operational effectiveness. Foam development can hinder the appropriate performance of devices, decrease the reliable use of resources, and make complex the tracking of important criteria. By applying defoamers, industries can effectively mitigate these concerns, causing streamlined procedures and improved efficiency.
Defoamers work by destabilizing the foam framework, allowing for rapid collapse and significant reduction in foam quantity. This activity not just improves the circulation of products through equipment, such as pipes, activators, and mixers, but also lessens disturbances brought on by foam overflow. Tools downtime is minimized, allowing for a much more constant and efficient manufacturing process.
In addition, using defoamers can cause lowered power usage. With much less foam to handle, compressors and pumps can operate more efficiently, causing reduced operational costs and an overall improvement in procedure throughput. Eventually, the strategic use defoamers not just addresses prompt lathering obstacles but likewise adds to a much more efficient industrial community, fostering an affordable advantage in a requiring market.
Improved Product Top Quality
The combination of defoamers in industrial procedures plays an important function in improving product top quality. By effectively regulating foam development, defoamers add to the consistency and harmony of end products. Extreme foam can bring about oygenation, which negatively affects the appearance and stability of formulas, specifically in markets such as food and drugs, beverages, and layers.

Moreover, defoamers facilitate much better blending and diffusion of active ingredients, causing homogeneity in formulations. This is necessary in applications where precise ingredient ratios are critical for efficiency and security. In addition, the elimination of foam can decrease the threat of contamination throughout manufacturing, further protecting item integrity.
Eventually, by improving item top quality, defoamers not only improve consumer contentment but likewise enhance brand credibility. Their function in maintaining high-grade requirements highlights their significance in modern commercial processes.
Cost Reduction Advantages
Carrying out defoamers in commercial procedures can bring about substantial cost reduction advantages. By efficiently managing foam formation, defoamers minimize product loss during production, thereby enhancing product usage. This reduction in waste converts straight right into reduced basic material costs, boosting general functional effectiveness.
Moreover, using defoamers can decrease power intake. Excessive foam can prevent tools performance, bring about increased power needs to keep production degrees. By reducing foam, defoamers promote smoother operations, permitting machinery to run extra effectively and decreasing energy expenses.
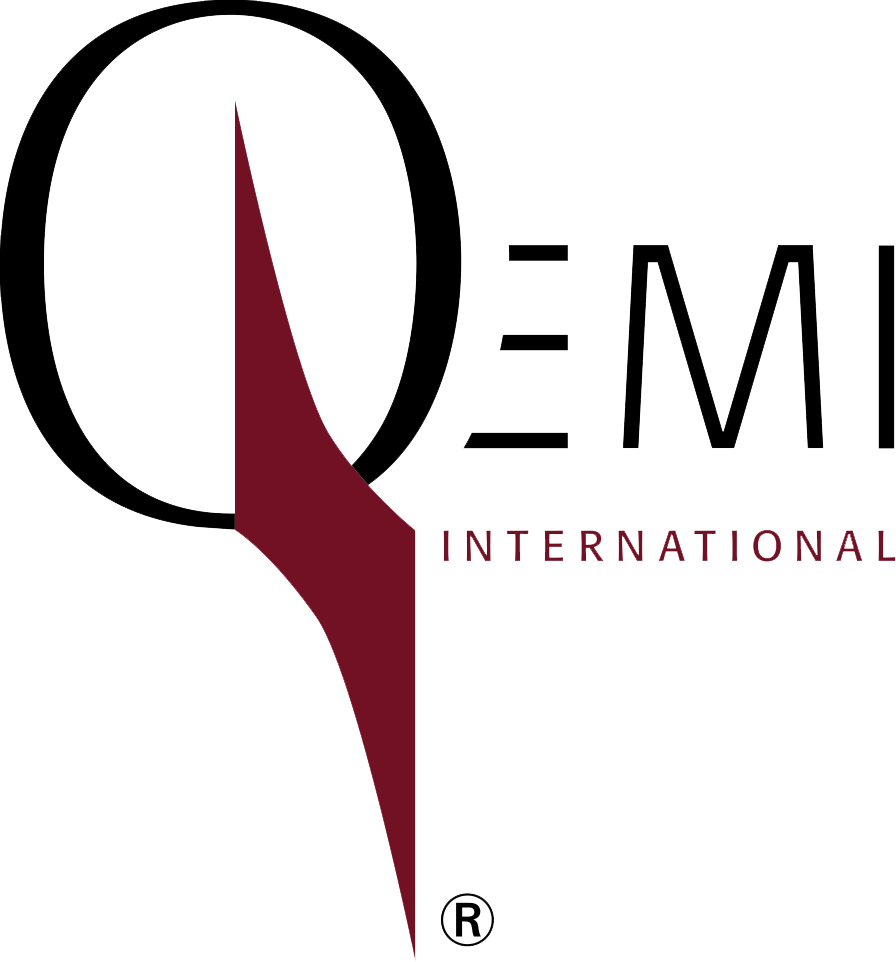
Additionally, defoamers can shorten processing times. Foam can produce extra challenges that prolong production cycles. By utilizing defoamers, sectors can simplify their procedures, bring about faster turnaround times and enhanced throughput. This performance not only increases manufacturing however also permits business to fulfill market needs a lot more swiftly.
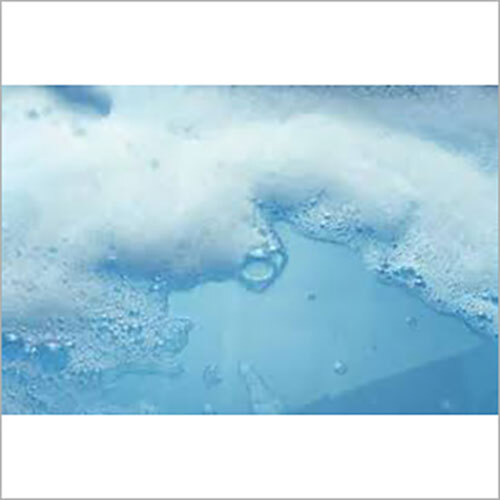
Environmental Impact Mitigation
In commercial processes, the use of defoamers plays an essential duty in mitigating environmental impacts related to foam generation. Foam can cause significant operational inefficiencies, causing increased emissions and waste generation. By efficiently regulating foam, defoamers aid maintain process performance, therefore reducing the general ecological impact of operations.
In addition, too much foam can overflow control systems, bring about spills that may pollute soil and water resources. Defoamers help reduce this risk by making certain that frothing does not go beyond recommended limitations, promoting compliance with ecological laws. This aggressive strategy not just safeguards environments but also improves the sustainability of check that commercial techniques.
Furthermore, the use of defoamers can reduce energy usage in different procedures. defoamers. Minimizing foam formation reduces the need for added energy-intensive procedures, such as raised anxiety or pumping, which might otherwise be needed to handle foam. As a result, the fostering of defoamers aligns with broader sustainability goals by advertising energy efficiency while decreasing the carbon footprint of commercial activities.
Eventually, incorporating defoamers right into industrial operations is a strategic step that supports environmental stewardship and liable source monitoring.
Convenience Across Industries
Across different markets, defoamers demonstrate impressive convenience, adapting to the details requirements of diverse applications. In the food and drink field, for example, defoamers are crucial to preserving item high quality by preventing foam formation during processing, which can affect appearance and flavor. In the pharmaceutical industry, defoamers guarantee the security of solutions, improving product effectiveness and consistency.
In the chemical production realm, defoamers promote smoother procedures by minimizing foam in response vessels, hence improving yield and lowering downtime. The paper and pulp market counts on defoamers to boost the effectiveness of pulp processing and paper manufacturing, guaranteeing optimum product integrity. Furthermore, in wastewater treatment facilities, defoamers play a vital role in managing foam throughout aeration procedures, resulting in better treatment end results.
The flexibility of defoamers expands to the oil and gas industry, where they assist in taking care of foam in drilling fluids and production processes. By customizing solutions to satisfy particular sector needs, defoamers act as indispensable devices that improve operational efficiency, product top quality, and overall procedure performance this contact form throughout a wide variety of fields. Their versatility highlights their worth in contemporary industrial applications.
Verdict
To conclude, the use of defoamers in industrial processes offers many advantages, including improved effectiveness, boosted product top quality, significant cost decreases, and positive ecological effects. Their ability to properly regulate foam development adds to operational connection and source optimization. Furthermore, the flexibility of defoamers across diverse industries highlights their important role in promoting sustainable Check Out Your URL techniques and success. The integration of defoamers stands for a calculated strategy to addressing challenges related to foam management in numerous producing environments.
Ultimately, the strategic usage of defoamers not only addresses immediate frothing difficulties but also adds to a much more efficient commercial environment, fostering an affordable advantage in a requiring market.
In industrial procedures, the use of defoamers plays a critical function in mitigating environmental impacts connected with foam generation. By efficiently managing foam, defoamers aid maintain process performance, thereby reducing the total ecological impact of procedures.
Additionally, in wastewater treatment centers, defoamers play an important role in controlling foam during aeration procedures, leading to better treatment results.

Report this page